|
Scotts Contracting St.Louis Design Build Sustainable Building Contractor-providing diversified quality service at a fair price. For all of your remodeling, repairs, and maintenance needs.
Search This Blog
6.19.2010
Catch and Stop-Energy Vampires
Wind Turbine Gearbox Reliability:
BP CEO Tony Hayward's testimony before the House Energy and Commerce
British press turns on Hayward, with plenty of anti-Obama rage thrown in for good measureMore from The Newsroom:
Fri Jun 18, 6:23 pm ET Many in the British press have slammed the U.S. government lately for demonizing BP, instead of simply holding the company accountable for the Gulf oil spill. But that sentiment has shifted noticeably since BP CEO Tony Hayward's testimony before the House Energy and Commerce committee Thursday. Hayward's inability (or unwillingness) to answer a number of direct questions about the decision-making that preceded the spill cost him many of his job responsibilities today — together with a good deal of his erstwhile cheering section in the British press. The Times (of London) didn't go easy on the oil executive, summing up its analysis of his performance in Washington with the headline: "From Mr. Bean to Mr. Has-been for BP's Tony Hayward." The Times' Giles Whittell wrote that Hayward "had a chance to save his career and the good name of his company by giving forthright, detailed answers to highly specific questions submitted in advance by two of the most astute and enlightened men in Congress." Instead, Hayward, he wrote, "seemed to have prepared by taking beta blockers." Whittell argued that Hayward stonewalled congressional interrogators, despite the executive's claims to the contrary. The Guardian clearly agreed with that assessment in its own piece on the hearing: "BP oil spill: Tony Hayward stonewalls Congress." Although Hayward was "carefully coached by legal and media teams and was testifying under oath," the Guardian noted, he "failed to satisfy." Also, according to the Guardian, Hayward delivered his answers "in flat, impassive tones." In the Telegraph, PR branding specialist Mark Borkowski wrote that "Hayward's communication skills didn't rival those of a tax inspector." "The new age demands a front-and-centre spokesman who can make the audience feel like he is listening and actually gives a damn," Borkowski wrote. "But Tony Hayward doesn't seem to have learned a great deal about being inclusive, about engaging with the public." "Accused of stonewalling, he stonewalled," Borkowski continued. "He couldn't, or wouldn't, answer most of the questions. In fact, he looked like a tired undertaker who was rather bored with having to look mournful." [PHOTOS: Haunting images of the oil disaster] Still, other British commentators had plenty of rancor left for the United States and its political leaders. Rupert Cornwell, a columnist for the Independent, added to the criticism that others in the British press have leveled against the Obama administration and Congress — that they're unfairly piling on BP even as the company tries to clean up its mess. Cornwell wrote that "yesterday's grilling of Mr. Hayward ... is a 21st-century version of the medieval stocks, public disgrace for the public villain of the moment." While Cornwell harkened back to medieval times to describe Hayward's treatment on Capitol Hill, the Daily Mail went back even further for a historical comparison. The British paper reported that Hayward was "subjected to a grilling so savage yesterday it was more like ancient Rome than Capitol Hill." "Wave after wave of criticism flew the way of the hapless boss and his company," the Daily Mail continued, "confirming them both as Public Enemy No. 1 in the U.S." The Economist, more highbrow than the typical Fleet Street tabloid, came out swinging at the Obama administration in the issue on newsstands Friday. However, the Economist's ire isn't motivated by jingoism or knee-jerk America-bashing — it's far too genteel for such tabloid sport. Instead, backed by its faith in free markets and neo-liberal trade policies, the Economist came out in support not just of a British company but of business itself, which it judged to be unfairly maligned in the spill fiasco. "America's justifiable fury with BP is degenerating into a broader attack on business," the Economist's editors wrote in today's lead editorial. The Economist expressed concern that business leaders who are "already gloomy, depressed by the economy and nervous of their president's attitude towards them" will likely not be encouraged by the treatment of BP. Because Obama's now pushing "firms into doing his bidding" — the magazine's characterizaion of efforts to hold BP responsible for an environmental catastrophe of its own making — the Economist draws parallels between the president and Russia's strong-armed former president and current prime minister. Hence the editors' new nickname: "Vladimir Obama." So while Tony Hayward is now a tarnished British hero in the Tony Blair vein, national morale may well rebound with the prospect of a good old colonial trade war — or Cold War, as the case may be. — Michael Calderone is the media writer for Yahoo! News. |
Solar Efficiency Breakthrough
Home > News Releases > University of Minnesota researchers clear major hurdle in road to high-efficiency solar cells
U of M researchers have cleared a major hurdle in the drive to build solar cells with potential efficiencies up to twice as high as current levels.
University of Minnesota researchers clear major hurdle in road to high-efficiency solar cells
Contacts: Preston Smith, University News Service, smith@umn.edu, 612-625-0552
MINNEAPOLIS / ST. PAUL (06/17/2010) —A team of University of Minnesota-led researchers has cleared a major hurdle in the drive to build solar cells with potential efficiencies up to twice as high as current levels, which rarely exceed 30 percent.
By showing how energy that is now being lost from semiconductors in solar cells can be captured and transferred to electric circuits, the team has opened a new avenue for solar cell researchers seeking to build cheaper, more efficient solar energy devices. The work is published in this week's Science.
A system built on the research could also slash the cost of manufacturing solar cells by removing the need to process them at very high temperatures.
The achievement crowns six years of work begun at the university Institute of Technology (College of Science and Engineering) chemical engineering and materials science professors Eray Aydil and David Norris and chemistry professor Xiaoyang Zhu (now at the university of Texas-Austin) and spearheaded by U of M graduate student William Tisdale.
In most solar cells now in use, rays from the sun strike the uppermost layer of the cells, which is made of a crystalline semiconductor substance—usually silicon. The problem is that many electrons in the silicon absorb excess amounts of solar energy and radiate that energy away as heat before it can be harnessed.
An early step in harnessing that energy is to transfer these "hot" electrons out of the semiconductor and into a wire, or electric circuit, before they can cool off. But efforts to extract hot electrons from traditional silicon semiconductors have not succeeded.
However, when semiconductors are constructed in small pieces only a few nanometers wide -- "quantum dots" -- their properties change.
"Theory says that quantum dots should slow the loss of energy as heat," said Tisdale. "And a 2008 paper from the University of Chicago showed this to be true. The big question for us was whether we could also speed up the extraction and transfer of hot electrons enough to grab them before they cooled. "
In the current work, Tisdale and his colleagues demonstrated that quantum dots—made not of silicon but of another semiconductor called lead selenide -- could indeed be made to surrender their "hot" electrons before they cooled. The electrons were pulled away by titanium dioxide, another common inexpensive and abundant semiconductor material that behaves like a wire.
Tags: Institute of Technology
"This is a very promising result," said Tisdale. "We've shown that you can pull hot electrons out very quickly – before they lose their energy. This is exciting fundamental science."
The work shows that the potential for building solar cells with efficiencies approaching 66 percent exists, according to Aydil.
"This work is a necessary but not sufficient step for building very high-efficiency solar cells," he said. "It provides a motivation for researchers to work on quantum dots and solar cells based on quantum dots."
The next step is to construct solar cells with quantum dots and study them. But one big problem still remains: "Hot" electrons also lose their energy in titanium dioxide. New solar cell designs will be needed to eliminate this loss, the researchers said.
Still, "I'm comfortable saying that electricity from solar cells is going to be a large fraction of our energy supply in the future," Aydil noted.
The research was funded primarily by the U.S. Department of Energy and partially by the National Science Foundation. Other authors of the paper were Brooke Timp from the University of Minnesota and Kenrick Williams from UT-Austin.
tags: Institute of Technology, Wisconsin -- Scotts Contracting scottscontracting@gmail.com http://www.stlouisrenewableenergy.blogspot.com http://www.stlouisrenewableenergy.com scotty@stlouisrenewableenergy.comSt Louis Renewable Feed
Featured Post
How Two Friends Turned Abandoned CASTLE into a 4☆HOTEL | by @chateaudut...
Join us on an extraordinary journey as two lifelong friends, Francis and Benoit, turn a crumbling, centuries-old castle into a stunning 4-st...
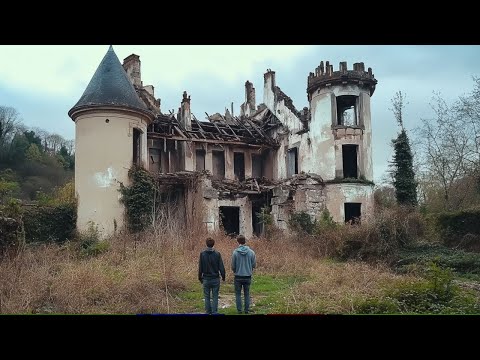
-
Thank You for stopping by the Green Blog. If additional information in needed or you have a question let me know by posting a question or ...
-
Convection is the movement of air in response to heat Warm air rises, cool air sinks. Because walls and windows are usually cooler than th...
-
Green Building Priority #6 – Ensure Durability Number 6 in my list of the top-10 green building priorities is to ensure that the home is dur...