Scotts Contracting St.Louis Design Build Sustainable Building Contractor-providing diversified quality service at a fair price. For all of your remodeling, repairs, and maintenance needs.
Search This Blog
Showing posts with label DIY. Show all posts
Showing posts with label DIY. Show all posts
2.19.2023
1.06.2022
7.27.2010
Do-It-Yourself Energy Audit
Do-It-Yourself Energy Audit: Go On, Try These Improvements Yourself!
Whether you Do-It-Yourself or choose to hire outside assistance, Build Green and do your part in reducing the US Oil Dependency- while becoming an Energy Wise User of Electricity!
If you find outside Assistance is needed-Scotts Contracting if available to Help. Scotty will provide a Cost Effective solution to your Home or Business Energy Needs. Click Here to Email Scotty for a No-Cost Free Green Site InspectionWhat is a Do-It-Yourself Home Energy Audit
As a homeowner you can easily perform your own home energy audit as there are many improvements that thousands and thousands of Americans have made in their homes to save energy. Below we have compiled a list of the critical areas in your home for you to inspect and take action on to fix in order to save energy. All of these suggestions require you to walk around your home and see how your home stacks up, then make the appropriate small home improvement.
D-I-Y Home Audit Checklist
HOME AREA
|
WHAT IS WASTING ENERGY?
|
HOW TO SAVE ENERGY?
| |
1
|
Lighting
|
Incandescent or halogen Light bulbs; lights turned on all the time
|
Switch to Compact Fluorescent Light Bulbs or LEDs; turn off lights in rooms that you're not using
|
2
|
Water Heater & Piping
|
Un-insulated
|
Upgrade or install insulation
|
3
|
Water Heater Thermostat Setting
|
Set to 125 °F
|
Set to 120 °F or lower
|
4
|
Electronics and small appliances
|
Left on when not using, plugged directly into outlets (but still using electric power even when turned off!)
|
Plug all electronics and appliances into power strips that you turn off when not in use (turning off power strip completely shuts off power use)
|
5
|
Heating & Cooling Equipment
|
Older than 10-12 years
|
Time to replace with energy efficient equipment; Install programmable thermostat; make sure air conditioner has proper amount of refrigerant
|
6
|
Forced Air Furnace
|
Dirty, old filter on the air intake
|
Replace or clean air intake filter once every 1-2 months during high use season
|
7
|
Electrical outlets, windows and window frames, baseboards, doors, attic hatch and wall/window mounted air conditioners
|
Air flowing in due to gaps or deteriorating of exterior caulking or weather stripping*
|
Apply new caulking, seal or weather stripping**
|
8
|
Exposed faucets, pipes, electric outlets and wiring
|
Cracks and holes in the mortar, foundation, and siding
|
Seal effectively with mortar or caulking to prevent any heat loss
|
9
|
Attic floor
|
Poorly insulated floor with gaps, thin insulation
|
Upgrade or install insulation including the attic hatch cover
|
10
|
Attic vents
|
Vent and interior air flow blocked by insulation
|
Clear vents of any insulation to help interior air circulation
|
11
|
All exterior corners of home; where siding and chimneys meet; and areas where the foundation and siding meet
|
Air flowing in due to cracks and holes in the mortar, foundation, and/or siding
|
Apply new mortar, sealer or siding to seal leak*
|
* To determine whether there is a gap for air to flow in any of these areas, consider the following: rattle your windows and doors to see if there is a proper seal; put your hand on seams or joints and see if there is any air flowing through them; and use the incense test: carefully (avoiding drapes and other flammables) move a lit stick along walls or potential openings and where smoke flutters, you have air sneaking in.
** When sealing your home, please be aware of backdrafting. Backdrafting is when various appliances and exhaust fans pull the combustion gases they emit back into the living space which can create an unhealthy situation in the home.
10.21.2009
DIY Solar Panels
Scotty writes:
I found the following article via
the web at the sites supplied below.
I hope you find the information usefull!
Build your own Solar Panel
Because I think that the price of a solar panel is still pretty high(in Europe), and because the stimulation from our government (in the Netherlands) is not so good (very,very complicated and time consuming) I started the project of building my own solar panel. I would like to invite anyone who has some experience with this or is interested in it ,to give me any advice or remarks about it. The main challenge is to build a panel that can withstand heat, cold, rain and hail for many years.
The First Solar Cells
After some experimenting and very long brainstorming about how to continue, I found another seller on Ebay who had the same cells (of which he gave the specification that they were 1,75 Wp each……) But these were slightly damaged. Well I decided to buy 500 cells ,a mix of 3 different qualities. The seller had not counted these cells but there were 620 cells, of which after a first selection , just over 500 were reasonably good. Not a bad deal to start with. And a lot cheaper! Also now I had over 100 cells for practice on soldering and handling.
Given the fact that the glass takes away about 10% of the power,without the glass it would have been about 17 Watt. I expect that during summer as the sun rises much higher above the horizon, the measurement will give higher readings , thus coming closer to the specifications…. I am using normal 4 mm (0.16 inch) glass because it costs me nothing. If you just look around near places were they renovate old houses you can get the old glass for free…… This compared to the real stuff they use for solarpanels which is quite expensive and probably very difficult to find.
The kit will have to dry for a few days, but anyhow the weather forecast does not indicate any sunshine the coming days………
Well, who feels like building panels also ? Or give me some advice, or share experience. I do not mind getting negative critics because they might be correct………and they are there to be solved !
Scotty writes:
I found the following article via
the web at the sites supplied below.
I hope you find the information useful!
I found the following article via
the web at the sites supplied below.
I hope you find the information usefull!
Build your own Solar Panel
how to build solar panels from scratch |
Because I think that the price of a solar panel is still pretty high(in Europe), and because the stimulation from our government (in the Netherlands) is not so good (very,very complicated and time consuming) I started the project of building my own solar panel. I would like to invite anyone who has some experience with this or is interested in it ,to give me any advice or remarks about it. The main challenge is to build a panel that can withstand heat, cold, rain and hail for many years.
Buying My First Solar Cells
In October 2008 I bought my first 100 cells via Ebay. But as I later learned, they were still very expensive: 300 Euros for 100 cells, including shipping. I was told they should produce 1,98 Watt each. Below a picture :The First Solar Cells
After some experimenting and very long brainstorming about how to continue, I found another seller on Ebay who had the same cells (of which he gave the specification that they were 1,75 Wp each……) But these were slightly damaged. Well I decided to buy 500 cells ,a mix of 3 different qualities. The seller had not counted these cells but there were 620 cells, of which after a first selection , just over 500 were reasonably good. Not a bad deal to start with. And a lot cheaper! Also now I had over 100 cells for practice on soldering and handling.
The 620 Cells! |
Building the First Small Panel.
Well I got started. Beginning with the soldering-technique, that takes some practice, but after a while you get the hang of it. And now my first small experimental panel is ready! The main focus and moreover challenge is to get the cells 100% sealed: air and water tight. The cheapest solution for me is to make a double-glass construction. And the cells in between the 2 plates of glass. The panel is made of 12 cells, each 0.55 Volts. On the picture below you can see many purple coloured wires. Those wires are each connected in between each cell so afterwards I can still do some measurements to compare each separate cell.My First Do-it-yourself Solar Panel! |
The First Measurements in the Sun
I must say that at first I was worried whether I would see the cells really produce the power they should. But after building a variable resistance (making it possible for me to roughly find the maximum power point) the sun at last was shining (not much sunshine here beginning of February) and I got my first real measurement : 15,5 Watt. According to the specifications the panel should give a maximum of 12 x 1,75 W = 21 Wp.Given the fact that the glass takes away about 10% of the power,without the glass it would have been about 17 Watt. I expect that during summer as the sun rises much higher above the horizon, the measurement will give higher readings , thus coming closer to the specifications…. I am using normal 4 mm (0.16 inch) glass because it costs me nothing. If you just look around near places were they renovate old houses you can get the old glass for free…… This compared to the real stuff they use for solarpanels which is quite expensive and probably very difficult to find.
Influence of Heating the Panel in the Sun.
During the first measurements, I found that the heating up of the panel was pretty strong. But this especially was the case for the backside. were the cells are glued upon (using the same kit I used for glueing and sealing the panel). This panel is 12 mm (0.47 inch) thick : 2 plates of glass each 4 mm (0.16 inch) and 4 mm in between. What troubles me is the temperature-difference between the front and backplate of glass. This will result in different expansions creating stress on the sealing,if that is repeated too often it will start leaking. Now I am using the same kit as is being used in solar panel factories. But it still worries me. A solution can be to keep the panels small, so the difference in expansion stays minimal.Improvements
A solution to the temperature-problem can also be to make the gap between the 2 plates of glass smaller. So the heat will be more evenly dissipated to both the front and backside ( thereby also creating more cooling capacity). My next panel (picture below) is the same size,the difference is the distance between the 2 plates of glass : it is now 1.5 mm (0.059 inch) …..and this also makes the sealing a lot easier and thereby better. I have used pieces of copper winding wire that I happened to have : 1.2 mm (0.047 inch) thick. I took several pieces of about 3 cm and spread them evenly along the side on the glass backplate. Then the kit along them all around the full edge. And finally pressed the front plate on it. The result is a gap between the plates somewhere between 1.2 mm and 1.5 mm. So on the inside, there is some trapped air (with, of course, a certain amount of humidity in it), which can potentially cause condensation. But my hope is that the amount of that is so small (only very small amount of air……) that it will not be a factor…… ( In the first panel I did put some stuff that can “eat” the condensation. I got this out of old double glass that I separated,the stuff is inside the aluminum strips between the double glass edges)The Improved Panel |
The kit will have to dry for a few days, but anyhow the weather forecast does not indicate any sunshine the coming days………
First Results
Bottom line is that if the output of each cell really hits 1,75 Wp then I can come to a price of Euro 1,20 per Wp (or even lower than that….) And with such a price the panel will not have to last for 20 years……..but off course that is my aim ! That will be the main challenge ! But I must say with this second panel my hopes are getting higher.Well, who feels like building panels also ? Or give me some advice, or share experience. I do not mind getting negative critics because they might be correct………and they are there to be solved !
- Do you like this article? Share it with others:
Scotty writes:
I found the following article via
the web at the sites supplied below.
I hope you find the information useful!
- “Build your own Solar Panels.
This website has been created to present the information I have learned from building my own solar panels. Using common household materials and tools, I was able to build quality panels as durable and efficient as commercially bought panels. Altogether the panels cost less than cheap panels of comparable wattage and I fully expect a long life from them....
...If you are mechanically inclined enough to cut plexiglass and wood to size, I am sure you will find this process much easier. If you are the type that worries about cutting everything correctly, this panel is much more forgiving, and you still end up with a high quality panel...”
First I started making a string with 12 cells connected in series.
You can see the jig I made for spacing the cells while soldering. It is a supermarket savings card, cut in pieces and super glued to Masonite.
You can see the jig I made for spacing the cells while soldering. It is a supermarket savings card, cut in pieces and super glued to Masonite.
Once I completed the 3 strings. I laid them out on a piece of glass.
I laid them out so they could be connected together in series.
I put small dots of epoxy in spots to keep everything from moving around. I didn't put any epoxy near the ends because I had to solder on the bus bars. I slid a piece of paper underneath the cells while I soldered on the bus bars, so no flux would get on the clean glass.
I laid them out so they could be connected together in series.
I put small dots of epoxy in spots to keep everything from moving around. I didn't put any epoxy near the ends because I had to solder on the bus bars. I slid a piece of paper underneath the cells while I soldered on the bus bars, so no flux would get on the clean glass.
I put the paper over the cells, and two small dots of epoxy in two corners on one side of the panel.
If you epoxy all four corners, the paper will wrinkle under vacuum.
If you epoxy all four corners, the paper will wrinkle under vacuum.
By putting the epoxy on one end it will let the paper flatten out to the side where there is no epoxy.
The epoxy keeps the paper from moving while you put the laminate over it.
The epoxy keeps the paper from moving while you put the laminate over it.
I then lay the glass, cells and paper on top of a piece of laminate. Adhesive side up. I try and center it within the laminate as best I can.
Next comes the laminate over the top. Adhesive side down.Make sure and lay it down as square as possible. Even with the epoxy the paper will move if you move the laminate over the top of it.
I hold the layers square with each other and start ironing together the laminate around the edges.
Its made the two sheets into a bag with a small opening at the bottom.
How I put the vacuum tube into the small opening. Its a hollowed out ball point pen. Seal it as best as possible.
I turn on the vacuum, and once all air is removed and the assembly is tight against the glass, I use a heat-gun and seal the laminate around the small opening for the vacuum.
I then heated the laminate to the paper side of the panel. I left the glass side alone, and once cooled down, cut the laminate off the front and sides.
To hook up the wires, I cut small slits through the laminate over the positive and negative bus bars. Only big enough to solder a wire, and directly in the middle of the bus bar. Be careful not to break the vacuum.
Once the wire is soldered on, I quickly cover the connection with JB Weld.
The laminate is actually adhered to the front on this one. I took it off later. It takes a long time for the glass to absorb enough heat to melt the laminate.
17.8 Volts DC, and a nice flat waveform.
Articles supplied by: http://www.olino.org/us/articles/2009/03/19/building-my-own-solar-panel
Subscribe to:
Posts (Atom)
St Louis Renewable Feed
Featured Post
How Two Friends Turned Abandoned CASTLE into a 4☆HOTEL | by @chateaudut...
Join us on an extraordinary journey as two lifelong friends, Francis and Benoit, turn a crumbling, centuries-old castle into a stunning 4-st...
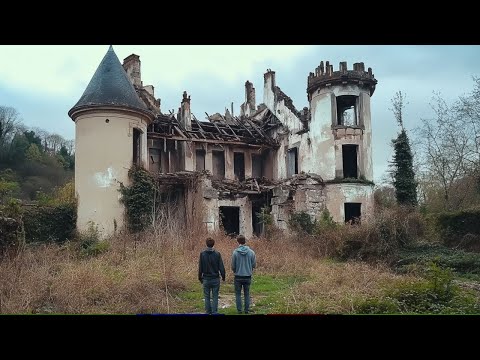
-
Thank You for stopping by the Green Blog. If additional information in needed or you have a question let me know by posting a question or ...
-
Convection is the movement of air in response to heat Warm air rises, cool air sinks. Because walls and windows are usually cooler than th...
-
Green Building Priority #6 – Ensure Durability Number 6 in my list of the top-10 green building priorities is to ensure that the home is dur...